CIP - Clean in Place
an industrial brewery equipment
CIP systems are critical in any and every Hygienic Process Plant. The success of the system depends upon its design in terms of flow, temperature, pressure, and concentration. Hypro offers a CIP system, centrally built or section-wise dedicated CIP systems. The CIP systems are carefully designed after evaluation of CIP requirements which vary from process to process as per soiling conditions. Cleaning devices available are chosen appropriately to suit the requirements and to ensure effective cleaning. When designing a CIP system for existing vessels, it’s just not the CIP system in itself BUT the vessel construction is evaluated to ensure effective CIP. In properly designed vessels leading to dead legs, inaccessibility to cleaning, shadows will ten to contaminate no matter how good your CIP Plant is.
Hygienic design and construction of pipework is key to an effective CIP Plant. There are several instances and possibilities for cross contaminations to occur in poorly designed or constructed pipework with dead legs. With its strong presence and proven designs, Hypro CIP stations take into consideration all design aspects to facilitate effective CIP. The CIP plants come loaded with adequate instrumentation levels to deliver the right temperature, flow, pressure, and concentration of CIP solutions to the equipment. With correct concentration, measurement water is also conserved during CIP by avoiding unnecessary drainage of water.
The tank configurations are selected based on CIP requirements followed by supply pumps, heaters. It’s also important to have the right type of pump for CIP Return and Hypro always uses a self-priming pump. The CIP systems come with pre-programmed CIP cycles loaded on the PLC to make it user friendly. Combinations are provided to facilitate different CIP cycles based on process conditions.
CIP systems circulate cleaning solutions in a cleaning circuit through pipework, machines, vessel, and other associated equipment. It is good practice to design equipment with fewer parts and no points that detergent cannot reach or where fluid accumulates; this will reduce cleaning time as well as save water, chemicals, and energy. This cleaning is done through cleaning devices Or Spray Balls provided in vessels etc. Pressure & flowrate at which CIP is getting Carried out is a very crucial part & needs to maintain to get effective cleaning of the tank. Various types of cleaning devices are used depending upon Tank diameter, Like Static Spray balls, Rotary spray balls, Cleaning Jets, etc.
Hypro CIP Tanks is designed in accordance with sound engineering practice & hygienic industry norms. The mechanical design of the tank is based on relevant ASME section VIII for dish shell & GEP. Where the code regulations are not precisely defined for a given situation, practical experience has been applied for.
- Process design (Heat transfer areas are based on a tailor-made computer-based program developed by our company & as per Hygienic Process Design & Practice.
- The tanks are suited for outdoor installation.
- All piping related to glycol, dome drain, and including cable conduits is routed through the insulation.
- The product piping is considered to be designed in accordance with a rigid piping concept with a flow plate.
- Cylindroconical Tanks with both cone ends are complete with Shell, top cone, and bottom cone.
- Tanks are insulated in case of Hot Water or Hot Caustic applications
- Thermo-wells 1 Numbers- For 1 Temperature Indicator on Shell.
- For Hot & Recovered water Tanks to know the temperature of the fluid.
- Cold Caustic/Acid /water tanks are neither insulated nor require a temperature transmitter
- All CIP tanks are provided with High- &Low-level transmitters to avoid overfill and empty runs
- Sample valve: – Simple diaphragm type sample valves provided so as measure concentration of fluid using sampling.
- CIP supply pipe from an operating level in the cellar to the tank top routed through the insulation.
- Dome drain pipe running from tank top up to the top of slab routed inside the insulating.
- Cable conduit pipes routed inside the insulation.
- Hygienic Process piping, fittings butterfly valves where ever required in
- OD based SS 304 material for Wort, Beer, Yeast, CO2 & Air vent, CIP S/CIP R.
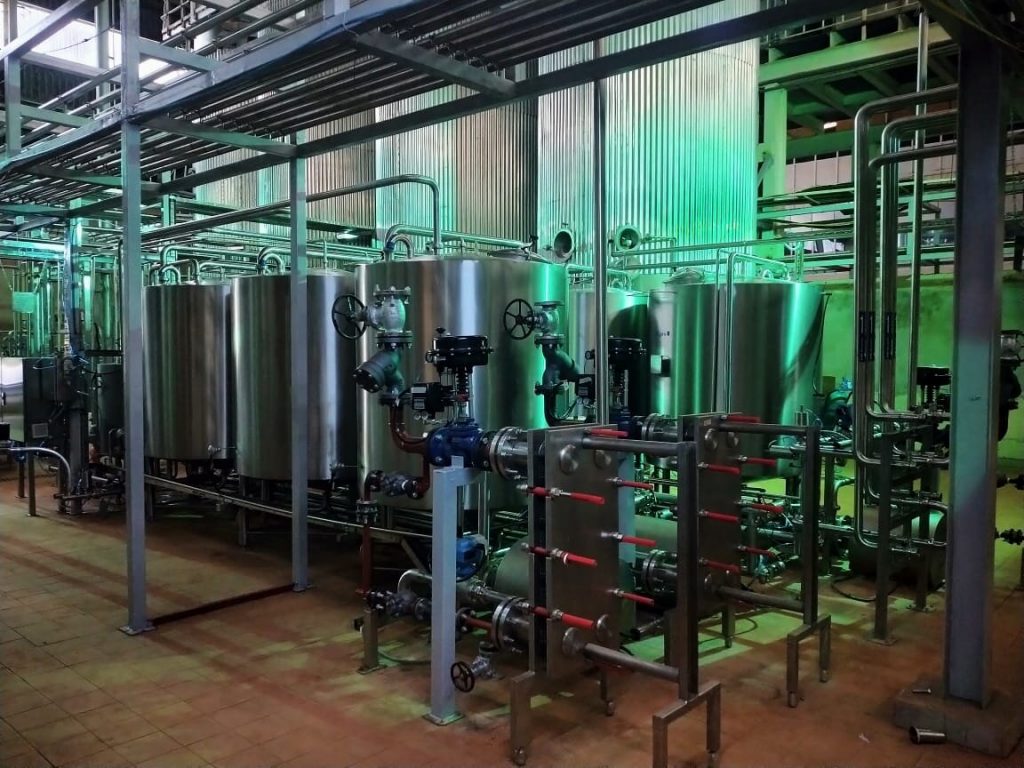
We would love to see you on social media!
Significance of CIP
After a batch of operation- inside parts, walls of vessels get accumulated with fluid, sticky material, foam, yeast, etc., which may form a layer over a period of batches making favourable conditions for germ & contamination. CIP frequency is completely dependent upon Brewers & operators, generally, once a week is preferred.
Hence In Brewery/Hygienic industry, there is a huge importance of the CIP section as vessels are directly been in contact with Food products, beverages. It is absolutely necessary to maintain a germ-free environment inside the vessel & ensure effective tank cleaning.
Standard Cleaning Sequence
- Pre Flush -Rinsing.
- Caustic circulation.
- Intermediate Flush- Rinsing.
- Acid circulation.
- Disinfectant circulation.
- Final Flush-Rinsing.