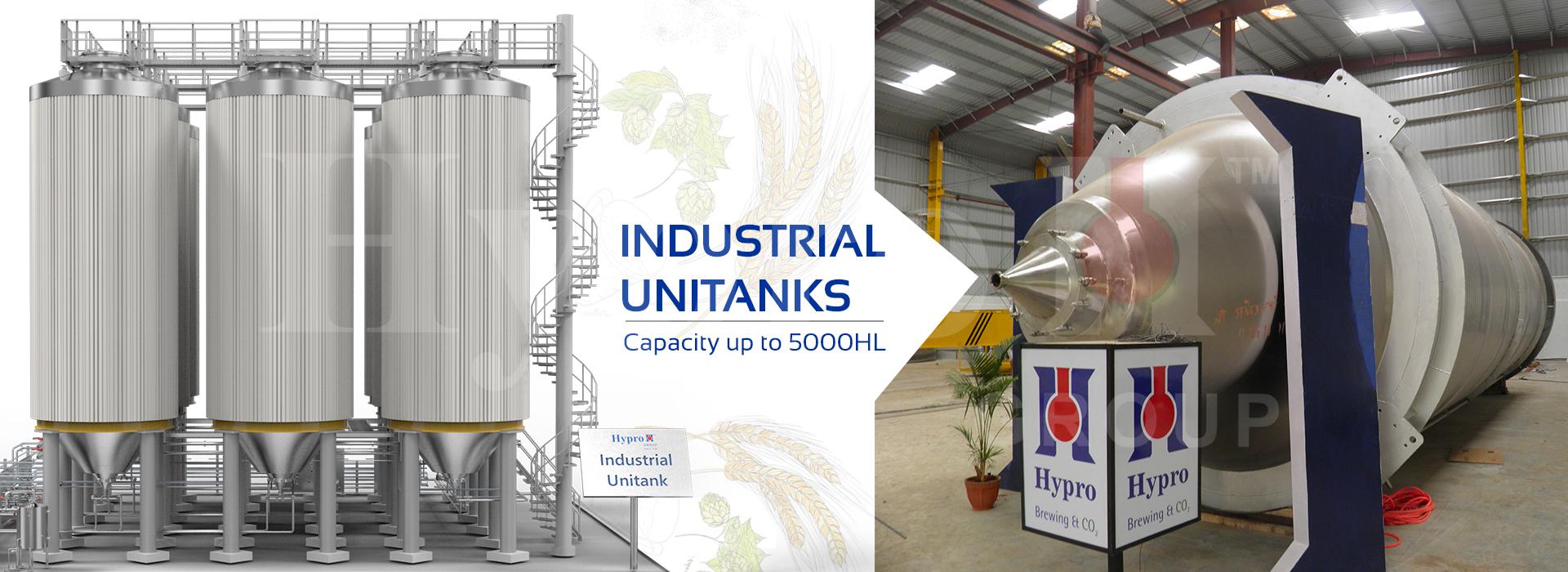
Industrial Unitanks
fully customized solutions
Hypro designs and manufactures up to 5000HL Unitanks/Fermentation Tanks in one piece in the factory. We also offer an on-site solution where road transport is a limitation. In such a case, tank components are assembled on site. Prefabricated surfaced finished top dished ends, bottom cone, the shell material is sent to site. Extended 5 years manufacturer guarantee speaks of reliability and peace of mind for our customers. Hypro has a qualified and experienced team to handle jobs of this nature. The automation system is well thought and selected right from sensors, controllers, and final control elements.
As the name indicates Unitanks are used in a brewery for three-unit operations/processes carried out in ONE tank. The unit operations/processes are:
- Fermentation of wort to produce green beer.
- Cooling down of green beer from fermentation temperature to maturation temperature.
- Maturation of beer to produce young beer
Aerated Cold wort from the brewhouse pitched with fermenting yeast is filled in the Unitanks batch-wise. (Normally 2-6 brews/tank). As the fermentation of the extract starts, it produces alcohol and CO2. Since the reaction is exothermic in nature, heat is evolved and is dissipated by circulating glycol in the cooling jackets of the Unitank. Temperature is automatically maintained in the Unitank by a PC-PLC based system. The control logic has been defined in the control logic document. At the end of the fermentation cycle, the first cooling cycle starts. In the first stage of cooling, the beer is cooled from fermentation temperature to 4 Deg C. At this temperature, the yeast settled at the bottom is collected from the Unitank and pumped to the Yeast Plant. After removal of yeast, the second stage of the cooling cycle starts where beer is chilled down to –10C. After achieving a temperature of –1 Deg C Maturation cycle starts and beer is matured in the Unitanks for a period of about 5-7 days. CO2 counter pressure is applied during this cycle to maintain the CO2 atmosphere in the beer and avoid oxygen pickup.
- Capacity from 50 L to 5000 HL
- Designed as per ASME Sec VIII Div 1 & latest hygiene standard
- Raw Material SS304L – European mills
- Complete cellar systems with flow plates
- Cooling rates-suit cooling cycles 24-48hrs
- Glycol circulation jackets designed for positive glycol circulation and low-pressure drop
- Machine ground surface 0.8-0.4Ra
- TTP-safety fittings & tank cleaning m/c imported from Europe
- Cellar Process & Utility Piping meeting hygienic standards making operations and CIP easier for the brewery over the years
- Platforms & Walkways which can be easily bolted on-site and no welding is necessary for assembly
- Tanks with welded cladding for bottom cone and a top dish which serves for longer life of insulation and better aesthetics
- Manholes and Top Plates for easy handling during production, also facilitates ease of cleaning to maintain good surface year after year
- PLC- SCADA based automation facilitates data logging, history, recipe management, and trends
- Brew iT – Data Management Software Tool, enables you to compare trends and parameters of various fermentation batches
- Outdoor Installation
- Reduce operator dependability
- Tank cleaning machine for low water consumption and high efficiency of cleaning
- Wort in: Connect the wort mains line to the Unitank bottom using Swing Bend. The valve on CIP – GAS line shall be kept open to release the air during wort collection in the Unitank. Chasing/Switching over from product to water or vice versa is done using a diverter valve with sight glass arrangement as shown in the P&I Diagram.
- CO2 Collection: Connect the GAS line to the CO2 collection header by using a swing bend and open valves on the lines. Usually done after achieving purity of 99.7 % v/v of the CO2 gas coming from the Unitank. Normally after 36 hours since the start of fermentation.
- Yeast Draw: Connect the yeast mains line to the Unitank bottom using a Swing Bend. The valve on CIP –GAS line shall be kept open to allow gas inlet to the Unitank to maintain positive gas pressure. Chasing/Switching over from product to water or vice versa is done using a diverter valve with sight glass arrangement as shown in the P&I Diagram.
- Beer out: Connect the beer mains line to the Unitank bottom using a Swing Bend. The valve on CIP –GAS line shall be kept open to allow gas inlet to the Unitank to maintain positive gas pressure for the supply of gas a CO2 the supply line is provided which can be connected by swing bend to the Unitank Gas inlet line. Chasing/Switching over from product to water or vice versa is done using a diverter valve.
- CIP of Unitank: After every batch, the CIP is done in Unitank. Ensure that during the CIP cycle liquid is pumped at an adequate pressure. (5.0 Bar at the pressure gauge on CIP Line with 15-17 m3/hr flow). There is a provision for CIP of Anti vacuum Valve on the top plate. This Valve is provided with a splash guard to prevent splashing on the top plate.
- Hot CIP of process lines: Its standard practice to carry out line CIP of all process headers (Wort, Yeast, CIP R). All process headers are cleaned & chased using HOT CIP & standard CIP cycles with required flowrates & pressure of 3-4 bars.
- CO2 Supply: A provision has been made to supply CO2 to the Unitank. The CO2 supply line can be connected to the Unitank by using a swing bend.
- Cylindroconical Unitanks are complete with Shell, top dish, and bottom cone.
- Cooling jacket embossed/dimpled type on shell portion and petal/embossed type on cone portion.
- Thermo-wells with shrouds on Shell and On Cone.
- Cooling section zones (as per the design) are on a shell and on the bottom cone.
- Sample valve: Membrane type Keofitt make with keyring – shrouds, drain for shrouds.
- CIP supply pipe from an operating level in the cellar to the tank top routed through the insulation.
- Dome drain pipe running from tank top up to the top of slab routed inside the insulating.
- Cable conduit pipes routed inside the insulation.
- Glycol supply and return piping from tank to Supply headers in SS 304 & routed inside the insulation. Glycol supply and return piping from main headers to supply headers in
- SS 304 with PUF insulation & SS 304 cladding.
- Lifting lugs with detachable arrangement for installing platform at site.
- Skirt with leg supports in MS hot-dip galvanized.
- Platform in hot deep galvanized material for the Unitank complete with railings.
- Hygienic Process piping, fittings butterfly valves where ever required in
- OD based SS 304 material for Wort, Beer, Yeast, CO2 & Air vent, CIP S/CIP R.
- The tank is having cooling jackets on the shell and cone portion.
- The temperature of the tank is indicated by temperature transmitters located at top of the shell and at top of the cone.
- Actuated butterfly valves are fitted for a tank to control the temperature of the tank.
- These valves will open or close to achieve a set temperature in profile/auto mode.
- Manual on/off facility is also provided which can be operated from the screen.
- This system is completely automated & operates from SCADA with defined control logic program.
- CIP Return Pump is trolley mounted & will start /stop based on steps of CIP cycle program defined for cellar CIP & line CIP of Equipment.
- Yeast cropping pump is also trolley mounted & automated operated from SCADA
- Yeast harvesting from Unitank & transfer to yeast section etc operations are from cycle selection through SCADA
We would love to see you on social media!
Most ideal fermentation conditions
with automaton

Manholes & Top Plates
Hypro has customized manhole designs for top and bottom and makes way for easy handling during production. The design facilitates ease of cleaning to maintain good surfaces year after year.

Internal Surface finish
The most important aspect during the manufacturing of the Unitanks. To ensure constant surface finish all over "Hypro" has automatic polishing machines that can handle shells, formed dished ends, conical ends. Internal and external polishing can be done with the machines which ensure smooth surfaces and good aesthetics.
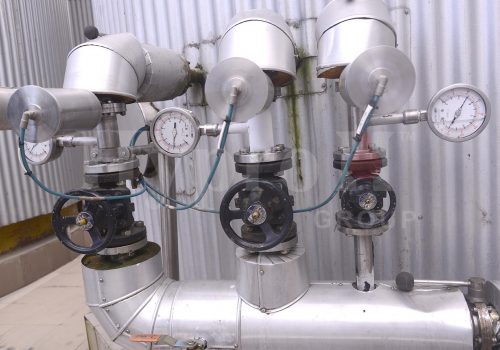
Cellar Process & Utility Piping
Cellar process piping meets "Hygienic" standards making the operation over years easier for the brewery from operation & CIP aspect. As a standard "Hypro" uses stainless steel material for piping of utility likes glycol or alcohol-water. Mild steel material is avoided although it has a cost advantage.

Platforms / Walkways
Platforms come in components that can be easily bolted on-site and no welding is necessary for assembly. As an option "Hypro" also offers platforms in Stainless Steel material which nearly eliminates mild steel or galvanized steel materials.

Tank Top Fittings
Tank tops come with reliable safety equipment from European suppliers. For cleaning of the tanks as a standard "Hypro" recommends tank cleaning machines which are heavy on first investment however they payback with water savings in due course.
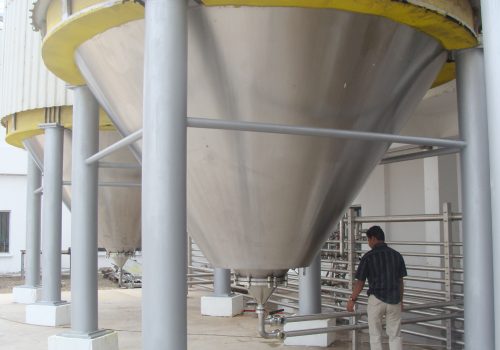
Cladding
As a standard "Hypro" always manufactures tanks with welded cladding for the bottom cone and top dish which in the end serves for longer life of insulation and better aesthetics.
Frequently Asked Questions.
This is an easy process. DO NOT use acid first. To remove any chemicals or welding lubricants from your new tank, you must first run a cleaning cycle with a caustic solution. We recommend running two separate cycles for absolute cleaning. Do not use an acid first, as a white residue will form. You must always clean your tank after receiving it from the factory.
The Unitanks do not have a spray ball included. The Unitanks come equipped with a 3″ TC Accessory port in which you could place a 3″ Spray Ball.
No, Unitanks do not have internal volumetric markings.
Although Unitank has the capability to serve beer directly, it is recommended that you transfer the beer to a dedicated serving vessel like a Brite Beer Tank or Keg to avoid the inadvertent contamination of fermentation by-product in the finished brew.
We test all our tanks for optimum quality before placing our 5-year warranty on them. This covers any issues with the tank’s function that would be considered a factory error. We also replace broken or faulty parts should this occur in the 5 year warranty period. We require photos of the damaged part(s) before helping with warranty related issues. If we determine it is an operator error we will not cover replacements or fixes. The warranty becomes absolutely void if you make any alterations or fabrications to the tank after purchase. We do not guarantee other people’s handy work.

Often Combined with
Hypro Fermentation Tanks provide exactly those assured conditions. They are tailored to the diversity of types and the specific system of fermentation parameter control operated by your brewery. Our vessels are designed with versatility, allowing all the brewery functions to be combined in fewer vessels for the economy, or separated into several vessels for increased capacity.