#CO2 #cement #Greenconcrete #Sustainability #CarbonNeutral
Low-Carbon Cement: The Next Big Leap in Sustainable Construction
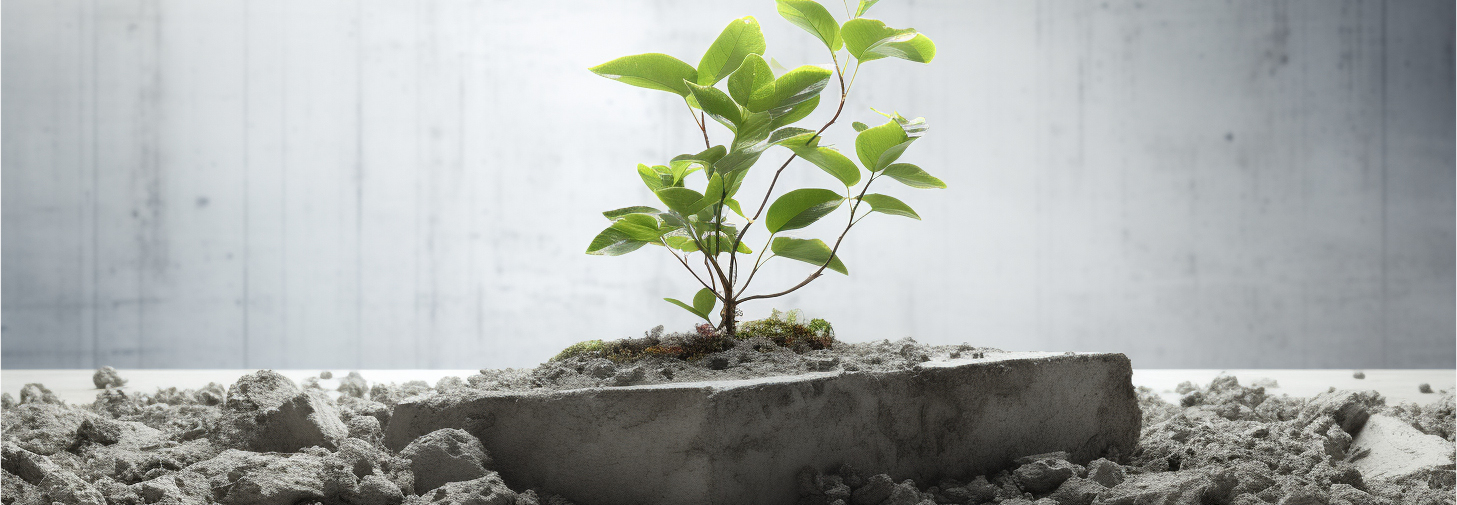
With mounting pressure to decarbonize, alternative materials and energy sources are making progress. However, these efforts alone won’t be enough. To truly revolutionize cement production, CO2 recovery innovations must work in tandem with these initiatives, capturing emissions before they reach the atmosphere and repurposing them for sustainable applications.
Rethinking Cement: What Defines Low-Carbon Cement?
Low-carbon cement is not defined by a single innovation but rather by a combination of strategic improvements across the production cycle. Alternative raw materials such as fly ash, slag, limestone calcined clay, and pozzolans are replacing high-emission clinker, significantly lowering the carbon footprint. The rise of blended cements and geopolymers is reshaping the industry by reducing reliance on carbon-intensive components while maintaining durability and performance.
The Game-Changing Technologies Powering Low-Carbon Cement
Beyond carbon capture, electrification is gaining traction as cement plants explore alternatives to coal-fired kilns. Hydrogen-based combustion is also being tested, offering a cleaner alternative with minimal environmental impact. Meanwhile, artificial intelligence and digital monitoring systems are optimizing fuel efficiency and reducing waste, ensuring that every aspect of production contributes to a lower carbon footprint.
Why CO2 Recovery is Essential, Not Optional
This is why CO2 recovery is not just an add-on – it is a necessity. Capturing CO2 directly from cement kilns prevents it from entering the atmosphere, while purification and liquefaction enable its repurposing across various industries. Carbon mineralization, which locks CO2 into cement products, not only strengthens the material but also reduces overall emissions. By integrating CO2 recovery, cement plants shift from being passive contributors to climate change to active participants in the circular carbon economy, transforming waste into value.
Cement Industry Pioneers: Who’s Leading the Way?
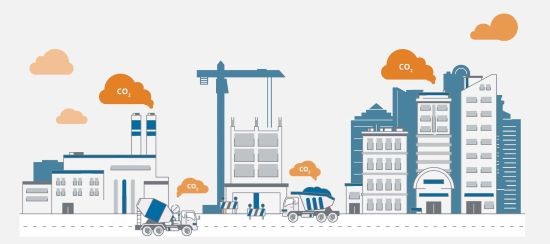
Carbon pricing, emission caps, and tax benefits for green technologies are encouraging cement manufacturers to adopt sustainable solutions. Regulations in Europe, North America, and parts of Asia are becoming increasingly stringent, reinforcing the notion that low-carbon cement is not merely an environmental commitment – it is a business imperative.
Hypro’s Role in Cement Decarbonization
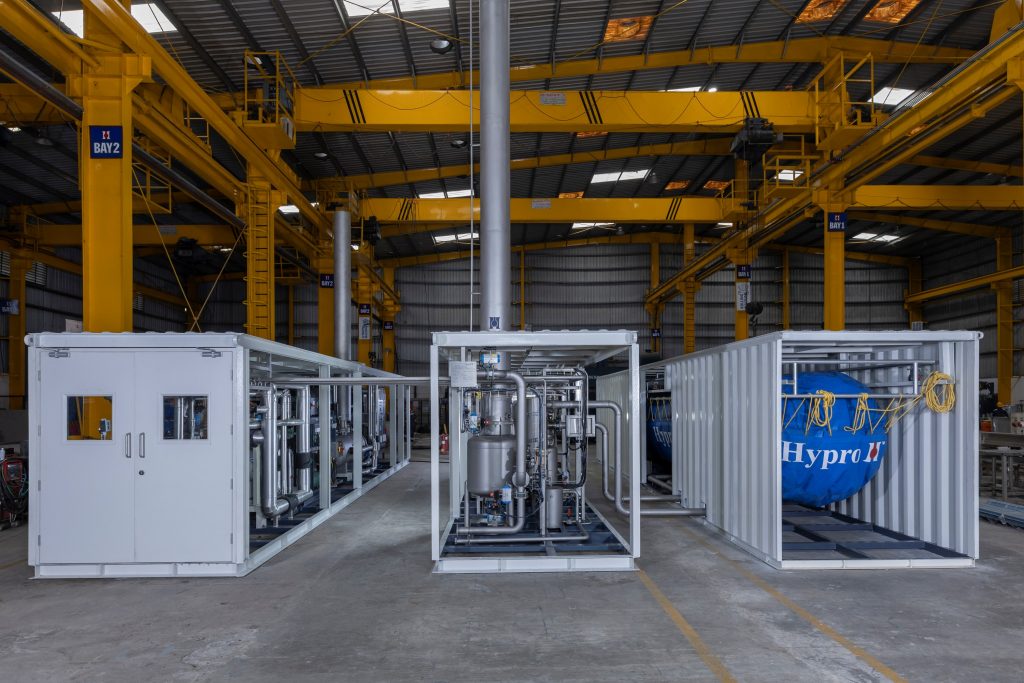
Are you ready to make the transition? Let’s build a sustainable, low-carbon future - one cement plant at a time.
The Road Ahead: Cementing a Sustainable Future
Related Posts
Engineering Sustainability
Hypro believes Earth Day is more than a moment - it’s a mission. From sustainability-driven innovations to CO₂ recovery and digital transformation, discover how Hypro...
Read MoreEnvironment First
On the World Environment Day, Hypro redefines the role of industry - not as a force that extracts, but as one that restores. With over...
Read More