#beer #CO2 #sustainability #circulareconomy
Industrial Brewery in Greenfield Setup - Turnkey & Sustainable
Setting up an industrial brewery isn’t just another CAPEX line item – it’s a defining moment in a company’s journey. One that blends vision with engineering, art with scale. And when that vision begins on a blank plot of land, it becomes more than a brewery – a legacy in the making.
A greenfield brewery isn’t a transaction. It’s a transformation. A rare opportunity to imagine every detail – from malt intake to fermentation flow – with zero legacy constraints. But such freedom demands precision.
Because in the world of brewing, precision is everything.
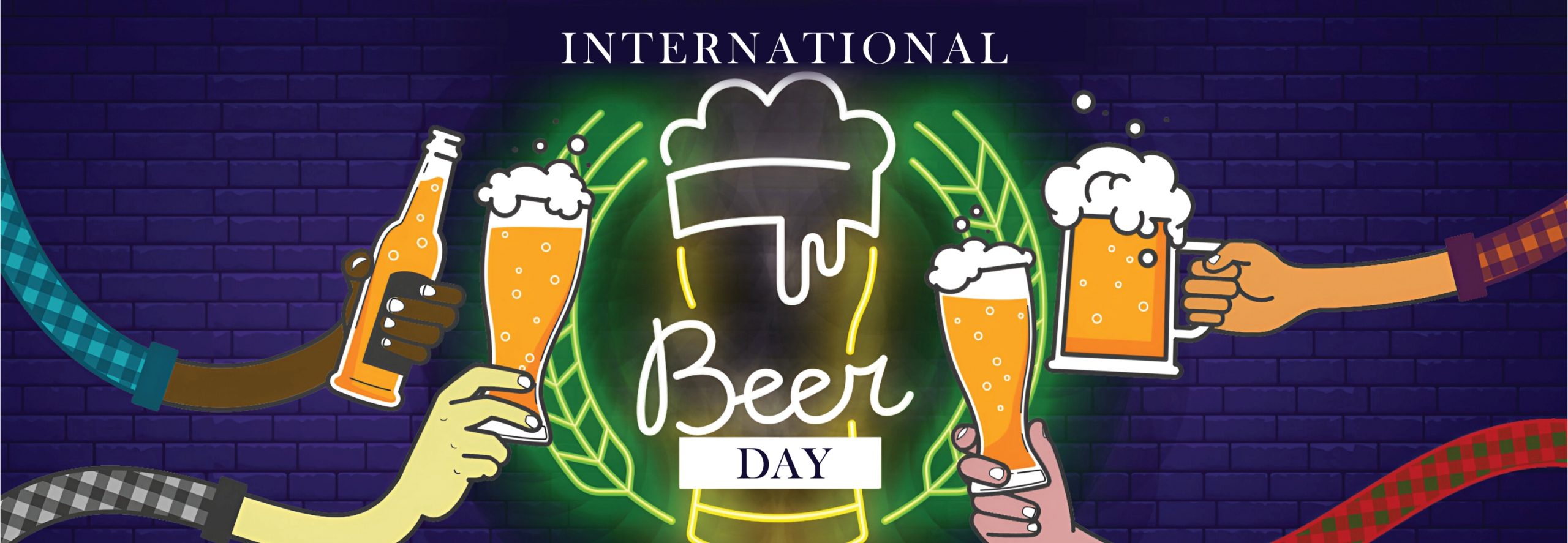
A misjudged brewhouse layout. A delay in utility integration. An automation mismatch. Each one is a silent saboteur. Not just on commissioning timelines, but on product integrity, energy efficiency, and commercial viability – on the brewmaster’s name on every bottle.
That’s why the world’s most ambitious brewers don’t gamble with fragmentation. They seek a turnkey brewery partner – one that carries both the soul of a brewmaster and the discipline of a systems engineer.
At Hypro, we’ve stood at that intersection – of vision and execution. Across continents and climates, across beer styles and brewing scales – we’ve helped global brewery groups bring their greenfield ambitions to life.
Because when you get the foundation right, everything that follows can flow – with confidence.
What Makes a Greenfield Brewery Truly Turnkey?
In the world of industrial breweries, the word turnkey is thrown around easily – often mistaken for a timeline, a handover, or a checklist. But when you’re building from bare land, where every choice will echo for decades, turnkey must mean more.
It must mean alignment – of equipment, energy, timelines, and vision. It must mean a system that breathes as one, from malt intake to final filtration. It must mean trust – not just in the outcome, but in the process.
At Hypro, a turnkey brewery isn’t a bundle of parts. It’s a living, flowing ecosystem, engineered from the ground up. From master layout and process design to brewhouse fabrication, cellar integration, and utilities – everything is modeled to serve both the brewmaster’s art and the owner’s scale ambitions.
Utilities don’t follow the process – they’re born with it. Steam, refrigeration, CIP, water systems – all integrated with precision from Day Zero. We take responsibility for installation and commissioning too, whether led by Hypro’s team or through our trained global partners.
Even automation isn’t bolted on later – it’s woven into the system’s DNA from the start, ready to be activated by Hypro’s proprietary platforms.
Behind all this is more than engineering – it’s assurance. Every industrial brewery designed by Hypro follows global codes: ASME Sec VIII Div 1 & 2, TEMA, EU, AD2000. Our systems are built to comply with U-Stamp and CE requirements – because when you serve global breweries, your standards must cross borders too.
And yet, technical perfection alone isn’t enough.
What defines a true turnkey partner is foresight. The kind that shows up in seemingly small things – like how Hypro’s Smart Wort Cooler quietly reduces energy use by up to 22%, cuts steam demand by 1.9 kg per HL of wort, and minimizes water consumption while recovering the exact amount of hot water needed across stages: mashing, sparging, chasing, and CIP.
It shows up in oxygen-free brewing water delivered by Hypro’s Deoxygenation Plant, achieving <10 ppb DO levels – critical for high gravity brewing and long shelf life.
It continues in how we respect tradition, with industrial brewhouses equipped for decoction brewing, where preserving flavor depth isn’t sacrificed for speed.
In yeast management, our turnkey delivery includes everything from yeast propagation plants and chilling-pitching systems to gravimetric metering – because every brew begins with a healthy culture.
Even CIP isn’t just a compliance box – it’s a fully automatic, PLC-based plant designed for reliability and hygiene without operator guesswork.
And for those who want to trial recipes before scaling, we offer HyMi – a microbrewery solution that mirrors the precision of industrial setups, empowering innovation without waste.
These aren’t just efficiencies. They’re convictions. They’re how Hypro turns process design into brewing intelligence – and execution into legacy. Because in brewing, what you overlook today becomes your burden tomorrow.
That’s why breweries who’ve been burned by fragmentation – the mismatched specs, the vendor blame loops, the silent downtimes – seek something better. They don’t just want supply. They want systemic harmony.
They want a brewery that performs not just on Day 1, but every day after.
And that’s the kind Hypro builds.
State-of-the-Art infrastructure, Inside and Out
Behind every world-class brewery built by Hypro stands a state-of-the-art manufacturing facility designed for precision and scale.
Spread across a 100,000 sq ft ground area with 40,000 sq ft of covered fabrication space, the infrastructure houses advanced equipment including dish pressing and spinning machines, shell rolling systems, automatic polishing units, and glass bead blasting capability – all under one roof.
This isn’t just about capacity. It’s about control – ensuring every vessel, seam, and surface meets the performance and hygiene standards Hypro is trusted for worldwide.
Watch the video below to step inside Hypro’s production floor.
In the Industrial Brewery, Fermentation Leaves No Room for Assumptions
Hygiene that lasts beyond commissioning
Hygiene isn’t how a tank looks on Day 1 – it’s how easily it stays clean on Day 1,000.
In an Industrial brewery that runs every day, hygiene is not a checklist – it’s an outcome of how equipment is built. If access points are awkward, cleaning becomes reactive. If cladding fails, insulation degrades. If welds are flawed, biofilms find a home.
That’s why Hypro uses SS304L from European mills, with welded cladding on both the cone and the dish to preserve insulation and aesthetics over time. Top plates and manholes are positioned for everyday use – because a clean system is one that’s designed to be cleaned, not just sanitised during FAT (Factory Acceptance Test).
And beyond what meets the eye, Hypro’s attention to detail extends to the very top of the tank — where safety, hygiene, and accessibility quietly converge.
Each vessel includes a dedicated CIP line to the anti-vacuum valve, thoughtfully equipped with a splash guard to avoid aerosol contamination on the top plate. The CIP supply pipe, smartly routed through the insulation from the operating level, ensures cleaning cycles remain efficient and thermally protected. Even dome drains and cable conduit pipes are internally routed through the insulation — maintaining not just thermal integrity but also aesthetic and hygienic discipline.
For thermal control, cooling jackets are provided on both the shell and cone, while temperature transmitters, strategically placed at the top of each, allow precise monitoring — because when you manage fermentation at scale, even a degree off-course isn’t just a deviation, it’s a defect waiting to unfold.
The cleaning paradox: Clean thoroughly or waste resources?
Industrial Breweries often face a false choice: over-clean and waste water, or under-clean and take microbiological risks. In modern breweries, CIP must deliver more than just chemical contact – it must do so with speed, reliability, and minimal waste.
Hypro’s CIP systems are calibrated for both efficiency and effectiveness. With minimal water consumption and maximum internal coverage, they close the gap between hygiene and sustainability – especially in a plant that runs 24/7.
The assembly bottleneck: Welding at site, delays in operation
On-site welding causes delays, safety risks, and cost overruns. Yet many equipment suppliers still deliver fermentation tanks that require field modification.
Hypro eliminates the friction with modular walkways that bolt on without welding at site, assemblies that cut installation delays. Hypro’s design thinking extends beyond fermentation, it supports seamless commissioning – a non-negotiable for any serious turnkey brewery project.
Whether you’re building a greenfield brewery or expanding an existing industrial brewery, the engineering decisions made around fermentation are the ones that define your future.
Because this stage doesn’t forgive shortcuts – it only rewards foresight.
In fermentation, there are no spare batches
There are no shortcuts. No easy fixes. No vessel that’s close enough.
That’s why Hypro doesn’t just supply fermentation tanks.
We design fermentation ecosystems – engineered with the foresight, technical rigour, and respect for process hygiene that only comes from building with brewers, not just for them.
Because when you’re building an industrial brewery or launching a greenfield brewery, the one thing you can’t afford to compromise – is fermentation.
Automation: Hypro’s Edge Over the Competition
In an industrial brewery, where multiple teams, shifts, and recipes collide, consistency cannot depend on human recall.
What happens consequently is not fermentation failure – it’s fermentation variability.
And in the absence of good data, every deviation becomes a mystery. That’s where in a turnkey brewery, automation should not be an afterthought bolted on later – it should be native to the process from Day Zero.
Hypro’s Unitanks are designed with PLC-SCADA-based automation from the ground up – enabling real-time control, recipe management, and batch-level data logging.
With Brew iT software, brewhouse steps like mashing, lautering, boiling, whirlpooling, wort cooling, and aeration are fully automated based on recipe selection — ensuring repeatability across shifts, seasons, and operators. But Brew iT goes beyond execution. It allows brewers to compare fermentation curves, track trends across batches, analyze deviations, and build reliable process knowledge over time — making confident decisions with insight, not instinct.
Hypro’s system architecture includes fail-safe designs with real-time feedback from valves and electrical components – minimizing manual intervention and reducing downtime risk.
And with built-in MIS (Management Information System), every process is captured, analyzed, and presented – giving plant heads the operational clarity they need, without waiting for audits or escalations.
Sustainability That Pays Its Own Way: CO₂ Recovery in Industrial Brewery
Every industrial brewery already produces what it later pays to buy.
Fermentation generates CO₂ – clean, abundant, and available at the source. Yet most breweries vent it, only to purchase commercial-grade CO₂ from the market for carbonation, packaging, and purging.
It’s a closed loop in reverse – wasting energy, money, and opportunity.
Worse, the costs aren’t just financial.
CO₂ prices fluctuate. Supply chains falter. Cylinder storage invites safety risks. And quality? It’s only as good as the last delivery.
In a turnkey brewery, where integration should drive efficiency, and in a greenfield brewery, where every system starts with a blank slate, ignoring in-house CO₂ recovery isn’t just a missed opportunity – it’s a structural flaw.
Closing the loop: From emissions to efficiency
Hypro’s CO₂ Recovery System captures CO₂ directly at the point of fermentation and purifies it to 99.998% v/v food-grade quality – ready for reuse in carbonation, purging, and packaging.
But Hypro goes further.
Our system also recovers CO₂ from non-brewing points of release – including pressurized tank transfers to filters and fillers. With the Counter Pressure Module integrated into the system, you don’t just recover CO₂ from fermentation – you balance and reclaim it across your utility line, where most breweries never look.
This two-module approach enables breweries to recover up to 85–90% of total CO₂ emissions – not just cutting waste, but recapturing value.
CO₂, reimagined as a performance metric
In a typical brewery setup, CO₂ consumption often hovers between 3 to 4.5 kg/hl. But with Hypro’s recovery and reuse system in place, breweries can gradually reduce that to 1.5 to 2 kg/hl – without compromising production.
The result?
A cleaner footprint, lower operating cost, and in many cases – a surplus of purified CO₂ that can be compressed and sold, transforming a utility expense into a revenue stream.
This isn’t theory. This is engineering made actionable.
Designed for integration, built for resilience
In a greenfield brewery, where utilities can be planned in harmony, CO₂ recovery should never be an afterthought.
Hypro integrates CO₂ recovery systems from Day Zero – alongside steam, refrigeration, CIP, and water – as part of a complete turnkey brewery solution.
The modules are compact, clean-in-place ready, and designed for minimal operator intervention.
For a plant head or project owner, this means fewer last-minute design compromises, better utility layout logic, and long-term self-sufficiency.
HySAAA: Hypro’s Sense Acquire Analyse Act Module
HySAAA ensures your plant remains in excellent condition, promoting longevity, efficiency, & safety.
Global Proof, Local Impact
Hypro has delivered advanced CO₂ recovery systems across 5+ continents and 25+ countries – from Carlsberg to Diageo, Bluntrock Brewery to Coopers, UB Brewery, Neustark AG, SABMiller, Molson Coors, and AB InBev.
Each one designed not just to meet sustainability goals – but to outperform them.
The CO₂ You Need Is Already in Your Process
Sustainability isn’t about sacrifice. It’s about not wasting what you already have.
That’s the kind of thinking Hypro brings to industrial and turnkey breweries – reclaiming CO₂ not as a green badge, but as a smart utility strategy that protects margins, safeguards quality, and supports long-term resilience.
Because when your own process can give you what you’re buying from outside – why not recover it?
Trusted by Greenfield Brewers Across Regions and Scales
They came with land.
Sometimes, just blueprints. Sometimes, only belief.
From Africa to Bhutan, Sri Lanka to India, breweries began not with bottling lines or fermentation tanks – but with a question: Can we build this right from the very beginning?
And Hypro answered – not with catalogs, but with clarity.
Not with individual vessels, but with end-to-end vision.
In Burundi, where infrastructure challenges test even the best engineering, Hypro delivered a fully integrated 100 HL cold block greenfield brewery. Not just installed – orchestrated. Fermentation, BBTs, utilities, and hygiene systems designed to perform as one.
In Sri Lanka, at Royal Cask Brewery, a compact yet ambitious 30 HL setup came to life under Hypro’s turnkey execution – crafted with the same foresight and hygiene logic applied to million-HL plants.
Further north in Bhutan, at the Namgay Heritage, a 20 HL brewery took shape – designed for diverse product flexibility and expandable to 125,000 LPM, proving that scale doesn’t always start big, but it must always start smart.
Back in India, the vision turned industrial.
At TRBEX IMPEX, Hypro executed a 100 HL / 300 hLPD greenfield plant – streamlined, efficient, and delivered with absolute process control.
At Abeera Beverages, a bold brewing facility began with a 200 HL brewhouse, built to scale all the way to 0.75 million HLPA – a system aligned from Day Zero for expansion, without architectural compromise.
Then came the large-format collaborations – where scale met scrutiny.
In Kolkata, Carlsberg India’s Parag Unit doubled its capacity from 0.35 to 0.7 million HLPA, with automation woven into every process line.
In Trichy, under the stewardship of Krones India, a 650,000 HL/year facility, expandable to 1.1 million HLPA, came to life-built with 400 HL brewhouse
equipment, Unitanks up to 3000 HL, and utility lines drawn like arteries around the process.
The story repeated itself in Hyderabad-500,000 HL/year, expandable to a million-where Hypro once again became the silent spine behind a fully integrated brewing system.
These aren’t just installations. They are systems – designed to breathe as one.
From Grain to glass
When you set up an industrial brewery, you’re not just buying tanks or piping.
You’re defining how your brand will taste, operate, and grow – every day, for years to come.
At Hypro, we don’t just deliver equipment. We build systems that sustain together and scale together – from the first trial brew to the millionth litre.
So, whether you’re building a greenfield brewery from the ground up or expanding an existing facility, ask yourself: Is your system just designed to run – or designed to perform?
If you’re ready to build something that lasts beyond timelines and outlives trends, Hypro is ready to help you make it happen.
Related Posts
CO2 Recovery Myths Debunked
Hypro's technology proves that craft breweries can achieve the same quality, efficiency, and operational benefits as large industrial breweries, debunking the myth that CO2 recovery...
Read MoreHops Processing
Explore the latest trends in hops processing, including sustainability, specialty hops, advanced technologies, and global market opportunities.
Read MoreEngineering Sustainability
Hypro believes Earth Day is more than a moment - it’s a mission. From sustainability-driven innovations to CO₂ recovery and digital transformation, discover how Hypro...
Read More